Innovation and Precision: Nicro’s Well Furnaces for Precision Engineering
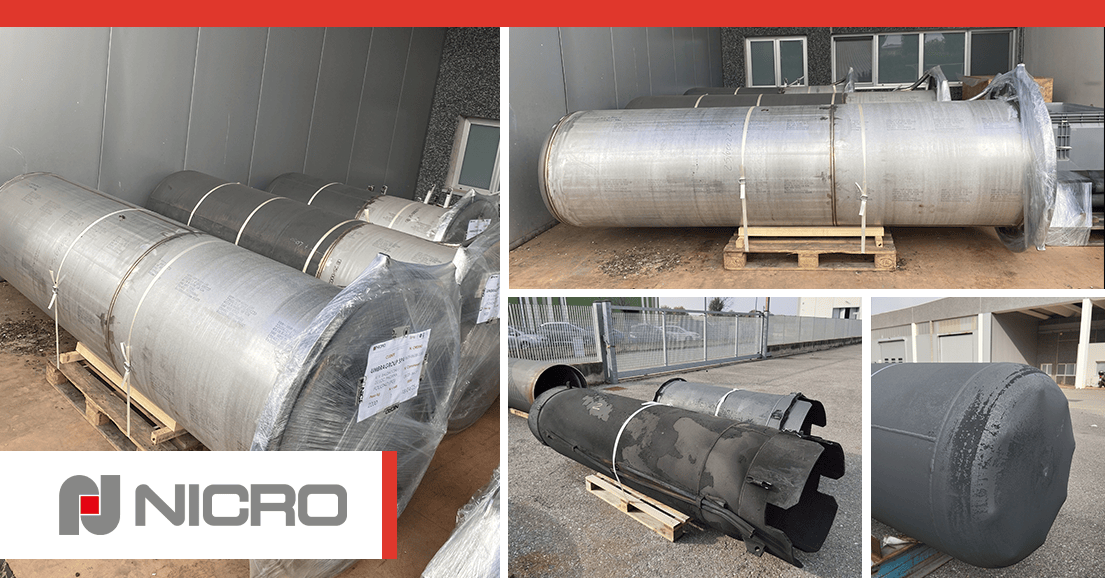
When precision, innovation, and technical expertise come together, the results are extraordinary. This is the case with the recent project completed by Nicro, a leading company in the production of high-nickel alloy steel components.
In collaboration with an Italian multinational in the precision engineering field (specializing in the design and production of bearings, actuators, balls, and recirculating screws for sectors such as aerospace and energy), Nicro successfully undertook a complex technical intervention on three well furnaces.
The goal? To restore 100% efficiency to worn-out components, providing the customer with significant savings and improved operational performance.
What are well furnaces and where are they used?
Well furnaces are essential industrial systems for the heat treatment of metals. Their cylindrical structure allows for the uniform heating of large components such as gears, shafts, and bearings, which are crucial in sectors like:
- Aerospace: For the production of high-resistance components for engines and structural parts.
- Energy: For elements exposed to extreme conditions, such as wind or gas turbines.
- Precision Engineering: For critical parts such as bearings and recirculating ball screws.
In the context of precision engineering, well furnaces are an indispensable resource for heat treatments that ensure uniformity and high performance—key aspects for the customer of this project. The client approached Nicro with the request to analyze the equipment of three well furnaces and restore their efficiency as much as possible through a careful evaluation of the components’ condition.
The challenges included:
- Assessing the damaged parts, aiming to replace only the severely compromised components, thus optimizing time and cost.
- Maintaining the high standards of the aerospace and industrial sectors, where precision and reliability are non-negotiable.
- Managing complex materials, including Alloy 330 (W.st 1.4864) and AISI 310S (W.st 1.4845), known for their heat and corrosion resistance.
Nicro’s Intervention on the Three Well Furnaces: A Detailed Overview
FURNACE 1
Materials: All main components (boiler, jacket, base spokes) are made of Alloy 330 (W.st 1.4864)
The intervention includes:
- For the retort, the flange and the first 100-150mm of the component will be recovered, along with about 1000mm of the base, to replace only the central part. The retort’s bottom will be repaired.
- The internal spokes will be rotated into a different position (after being properly sandblasted for cleaning and welded where necessary) to distribute the load more evenly, even on the intact base part.
- The jacket will be completely rebuilt, as it is excessively deteriorated, thanks to a customized design tailored to the specific client’s needs.
FURNACE 2
Materials: Boiler and spokes in Alloy 330 (W.st 1.4864); jacket in Alloy 330 (W.st 1.4864) and AISI 310S (W.st 1.4845)
The intervention includes:
- Recovery of the flange and the first 100-150mm of the retort, while the rest of the component will be reconstructed.
- Complete replacement of the jacket with a custom design intervention.
- Full recovery of the spokes, which will be sandblasted, cleaned, and positioned with the necessary welds.
FURNACE 3
Materials: Boiler and spokes in Alloy 330 (W.st 1.4864); jacket in Alloy 330 (W.st 1.4864) and AISI 310S (W.st 1.4845)
The intervention includes:
- Recovery of part of the retort (flange, the first 100-150mm, and about 700mm of the base), with complete replacement of the central part. The retort will be repaired at the bottom, with rotation of the internal spokes and general refurbishment of the existing welds.
- The jacket will be recovered and sandblasted.
- The internal spokes will also be sandblasted and welded where necessary, positioned with a new orientation to distribute the load more evenly, thus reducing the strain on the jacket repairs.
By following this approach, the client will not only benefit from high-performance components but also reduce waste by replacing worn-out components only when absolutely necessary, maximizing both efficiency and cost savings by fully recovering reusable parts.
This project highlights Nicro’s cross-functional expertise, capable of working on an international scale thanks to its excellent technical and engineering capabilities, along with an approach focused on efficiency and sustainability.
Do you have a complex project to execute? Contact Nicro and find out how we can make a difference.